News & Insights
Energy planning for food and beverage manufacturers
As F&B manufacturers work to integrate ESG objectives into core business operations, they need practical yet strategic methodologies for boosting energy efficiency, embracing renewable resources, and realizing carbon reductions. This article highlights the transformative impact of energy planning in enabling F&B manufacturers to achieve the environmental component of their ESG commitments.
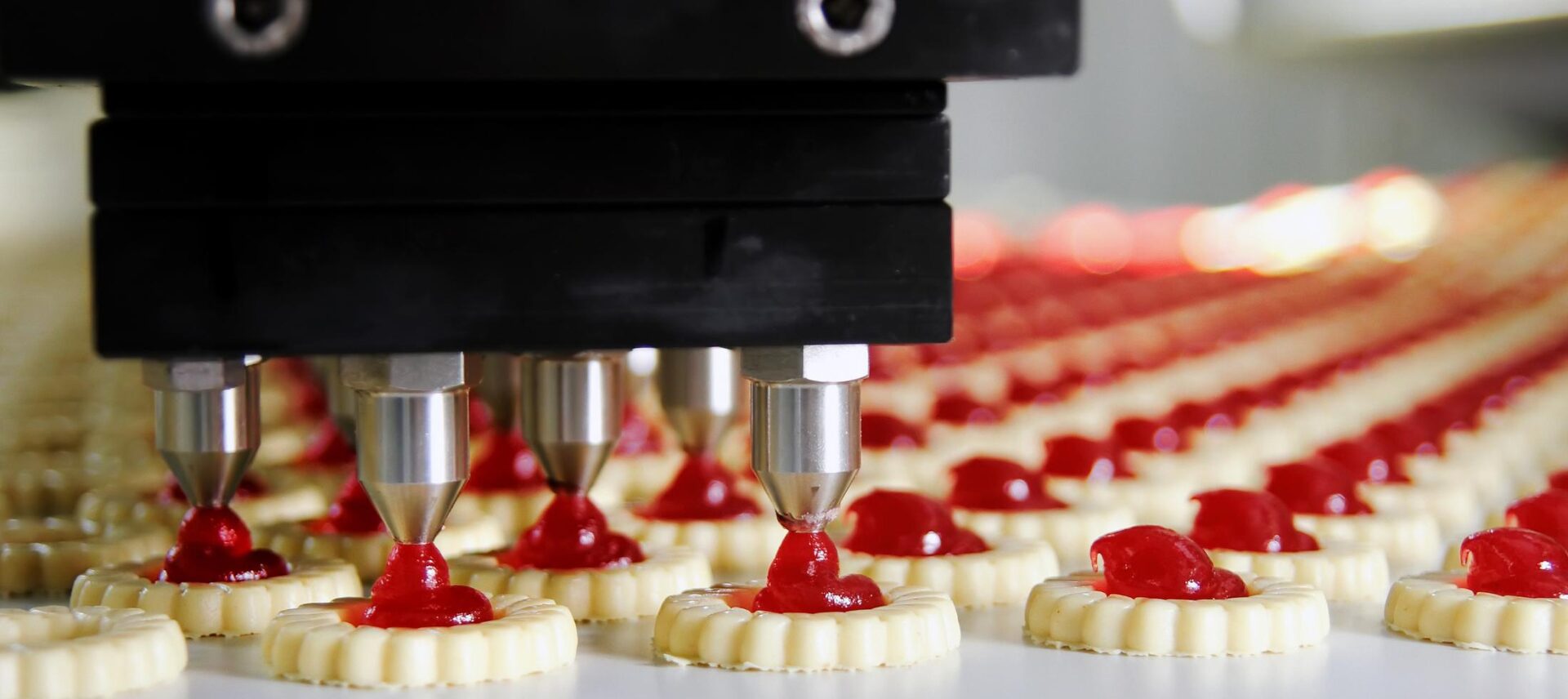
In the food and beverage (F&B) sector, manufacturers are constantly adapting to meet evolving consumer expectations. This pursuit is intrinsically linked to managing energy costs, promoting environmental stewardship, and embracing decarbonization. These goals reflect not only market demands but also an internal drive toward more sustainable practices.
F&B manufacturers navigate a complex ecosystem, marked by increased production demands and escalating energy requirements. As these pressures mount, the importance of strategic energy management becomes undeniable.
Energy challenges for food and beverage manufacturers
These are just some of the unique issues that food and beverage manufacturers face when it comes to managing energy:
High energy consumption. The F&B industry demands substantial energy input, especially for heating, cooling, sanitation, and refrigeration. This energy-intensive nature underscores the need for efficient management to sustain operations without compromising production quality.
Fluctuating energy costs. The dependency on consistent energy supplies makes F&B manufacturers particularly vulnerable to volatile energy prices. Such fluctuations can drastically affect operational costs and, consequently, profitability.
Regulatory compliance. With environmental regulations becoming increasingly stringent, F&B companies are compelled to invest in cleaner and more efficient technologies. This shift is not only a regulatory response but also a step towards future-proofing their operations against more severe regulations expected down the line.
Corporate ESG Initiatives. Efficient energy management plays a pivotal role in the ‘environmental’ component of ESG, as it directly influences a company’s carbon emissions placing a priority on the quality of the energy sources used.
Legacy systems and waste. Many F&B facilities operate with outdated processes and equipment, leading to significant energy inefficiency and waste. The challenge lies in upgrading these legacy systems without disrupting productivity.
Lean budgets. Operating within tight capital and operational budgets is a critical concern for F&B manufacturers. There is a constant balancing act required to maximize profitability while investing in necessary technological updates and energy-efficient practices.
Navigating this energy landscape effectively not only addresses immediate hurdles but also opens doors to sustainable growth and a competitive edge.
Deeper wins in energy planning for food & beverage manufacturers
Most well established F&B manufacturers have been proactively implementing resource management strategies for a long time. After all, F&B is inherently dependent on natural resources. (When making beer, it’s a solid business practice to make sure quality water and barley will be available well into the future.) And most have already made dramatic reductions in energy and water usage.
Here are some of the deeper wins available for F&B manufacturers:
Audit the manufacturing process
While many plants have realized significant gains through capital upgrades to facilities, substantial opportunities still exist in optimizing manufacturing processes. A detailed process audit can uncover inefficiencies—even in well-run facilities. By systematically evaluating each step of the manufacturing process, companies can identify inefficiencies such as excessive energy use during downtime or redundant processes that contribute to higher energy consumption. Implementing more streamlined operations can result in considerable energy savings and improved productivity.
Address deferred maintenance
Often overlooked issues like leaks (steam, air, and water) might appear minor but have a substantial cumulative impact. For example, a steam leak might necessitate additional cooling efforts, which increases energy consumption significantly. Addressing these maintenance issues prevents not only physical losses but also helps cultivate a proactive culture among operators, encouraging them to engage in energy conservation measures more earnestly.
Metering and tracking
Installing meters to control and track consumption facilitates data-driven decision-making. Establishing key performance indicators (KPIs) and setting targets based on these metrics can guide a facility’s energy management strategy. Over the course of a year, data collected can highlight specific behaviors—such as doors remaining propped open or unnecessary water usage—that lead to energy waste. If a plant lacks advanced metering infrastructure, starting with analysis of energy bills is a practical first step toward understanding and managing energy usage patterns.
Manage peak loads
Using advanced Utility Management Systems (UMS) can significantly enhance the ability to monitor and control energy usage in real time. These systems can integrate seamlessly with existing production processes, allowing for the identification of inefficiencies and the improvement of energy allocation. Some manufacturers implement peak shifting strategies to minimize energy costs during high-demand periods, thus optimizing overall energy expenditures.
Find the equipment opportunities
A detailed walkthrough by a dedicated team that examines each step of the manufacturing process to compile a comprehensive list of energy-saving opportunities, can generate options to be evaluated for impact and feasibility. This process can optimize already scheduled equipment replacements and result in finding force multipliers for energy efficiency and reduced costs.
Upgrade cooling, heating, and cleaning processes
As F&B manufacturers look to overcome the challenges of energy efficiency, significant opportunities arise in refining operational fundamentals. Upgrading how things are cooled, cleaned, and heated can redefine energy use within the industry, including:
Upgrade cooling processes
Cooling systems are among the highest energy consumers in the F&B industry. Implementing advanced refrigeration technologies (such as cascade systems or transcritical CO2 systems) can offer greater efficiency and a reduced environmental impact compared to traditional HFC systems. However, optimizing the layout and scheduling of cooling operations can also help avoid peak energy rates and lead to significant cost savings.
Enhance cleaning efficiency
The cleaning of production equipment and facilities often requires substantial amounts of both heat and water, making it a prime target for energy savings. Employing high-efficiency cleaning systems, such as Clean-In-Place (CIP) systems, can minimize the use of these resources. These systems recycle cleaning solutions and water, and precisely control temperatures and flow rates to ensure optimal cleaning with less energy.
Explore innovative heating techniques
Heating processes can also be optimized by adopting more efficient technologies like heat pumps, infrared warehouse heating, and induction ducts which use a fraction of the energy of traditional steam systems. Geothermal and aerothermal heat pumps provide sustainable alternatives to both heat and cool buildings, depending on the season. Furthermore, reevaluating and improving insulation on pipes, tanks, and in building envelope ensures that heat is preserved, reducing the need to generate additional energy.
Mechanical vapor recompression
An often overlooked yet highly effective strategy in industrial energy efficiency is Mechanical Vapor Recompression (MVR). This technique plays a crucial role in processes like evaporation and distillation, which are prevalent in food and beverage manufacturing. Low-pressure residual steam can be compressed and upgraded to higher pressure and temperature steam that can be reused to meet the process heating needs. This method enhances energy efficiency and reduces operational costs by harnessing existing energy flows within the production cycle.
Integrate heat recovery
Introducing heat recovery systems into existing HVAC systems can capture waste heat from operations like refrigeration condensers or compressors and use it to preheat cold air make-up. This not only conserves energy but also reduces the operational costs associated with heating air from a cold start. Another method is to implement heat exchangers within the sewer infrastructure to extract the heat of wastewater effectively transforming an overlooked resource and use it to preheat water or vaporize process gases like CO2 instead of using steam. This method enhances energy efficiency and contributes to reducing environmental impact by leveraging existing resources.
As F&B manufacturers streamline their cooling, cleaning, and heating processes, the logical progression leads to an exploration of self-sufficiency in energy production. Generating electricity onsite emerges as a transformative strategy for those aiming to gain complete control over their energy usage and costs.
Add onsite power generation and efficient energy resources
While implementing onsite power generation involves a significant initial capital investment, the ability to produce and distribute power sustainably and independently presents an attractive proposition. This strategic step forward not only underscores a commitment to sustainability but also enhances self-reliance, positioning food and beverage manufacturers to better control their energy futures. By reducing dependence on external power sources, companies can stabilize their energy costs and improve operational resilience.
Here are onsite generation strategies for F&B manufacturers:
Solar power solutions
Utilizing solar energy through photovoltaic systems is one of the most straightforward methods for F&B facilities to generate power directly onsite. These systems convert sunlight into electricity, providing a clean, renewable source that can significantly reduce electricity bills. Additionally, solar daylighting technologies, which enhance natural light within facilities, can preheat spaces and materials, further reducing the need for artificial heating and lighting.
Solid oxide fuel cell (SOFC) generators
SOFC power generators represent cutting-edge technology in the field of onsite power generation. These systems produce electricity through a chemical reaction between oxygen from the air and a fuel, such as natural gas or biogas. SOFC generators are highly efficient and can substantially lower greenhouse gas emissions when compared to conventional power sources.
Geothermal / geo-exchange
By utilizing the earth’s stable underground temperatures, geothermal systems can efficiently heat and cool buildings, reducing overall energy consumption. Although geothermal installations generally require more upfront space for a well field, vertical drilling options can significantly reduce surface area usage while delivering the same energy benefits, allowing more sites to leverage this sustainable energy source without large-scale land disruption.
Hydrothermal energy systems
Incorporating hydrothermal heat pumps into an energy strategy harnesses natural heat from water sources nearby. This technology is particularly effective for not only heating but also cooling purposes, offering an excellent example of how initial investments in energy efficiency can lead to substantial long-term savings and environmental benefits.
Advanced nuclear options
Exploring ultralight nuclear reactors, also known as small modular reactors (SMRs), offers a promising, albeit more complex, avenue for onsite electricity generation. SMRs provide a consistent power output and have a smaller footprint than traditional nuclear facilities, aligning with the industry’s needs for reliable and clean energy sources.
Energy storage systems and microgrid implementation
With onsite electrical generation comes to the opportunity to incorporate energy storage solutions ways to interface with the main electrical grid so that manufacturers can store excess electricity generated during low-cost periods to use during peak demand times. This helps in managing energy costs more effectively and ensures a continuous power supply, especially critical during unplanned grid outages.
While a range of onsite power generation options are available, implementing these solutions, whether through deep retrofits or planning for new capacity, demands a comprehensive approach to energy management. Effective energy planning is essential as it addresses the complexities of enhancing efficiency without disrupting ongoing production—a delicate balance that requires thoughtful coordination and strategic foresight.
Getting started with energy planning
A well-structured energy plan not only outlines effective ways to integrate renewable energy sources and upgrade existing systems but also sets a clear roadmap for achieving energy efficiency at scale. By prioritizing strategic investments and finding the low-hanging fruit, F&B manufacturers can enhance operational resilience and cost-effectiveness.
Here are considerations when getting started:
Whole process thinking. Each F&B manufacturer’s context is distinct, necessitating a tailored approach to evaluate operating risks, capital and operational expenditures, and sensitivity to ongoing volatility in energy pricing. Initial discussions in energy planning lay the foundation for understanding that every investment, whether capital or operational, must align with the organization’s strategic priorities and timeline. This phase is mostly conversational and requires an acknowledgment that all initiatives will involve some level of investment.
Measure to find the baseline. Establishing a clear baseline is crucial for measuring progress. This involves assessing current energy usage and identifying areas for improvement, which serves as the benchmark for future energy-saving efforts and investment justifications.
Regulatory and incentive exploration. Many regions offer subsidies, tax incentives, or feed-in tariffs specifically designed to support renewable energy projects. These financial incentives can significantly reduce the burden of initial investments, making sustainable projects more feasible and attractive.
Employee engagement and culture shifts. A successful energy plan engages every level of the organization, creating a culture of energy consciousness and innovation. Encouraging employee involvement in the process and rewarding departments that achieve energy goals are effective strategies for fostering commitment and driving continuous improvement.
How Salas O’Brien can help
Effective energy planning is not static but adaptive, incorporating new technologies, practices, and insights to continually refine and improve energy strategies. Regularly updating the energy plan in response to technological advancements and market changes ensures that F&B manufacturers remain at the forefront of energy efficiency in their own context.
Salas O’Brien can provide a breadth capability that is unique. We provide support from initiation of the process to developing the economic model and provide technical expertise for implementation and ongoing measurement and commissioning, allowing you to rely on a trusted partner to help you reach the right decisions and implement high-performance energy strategies for your organization.
To discuss your project, reach out to one of our contributors below.
For media inquiries on this article, reach out to Stacy Lake, Director of Corporate Communications
Sustainability for F&B manufacturers
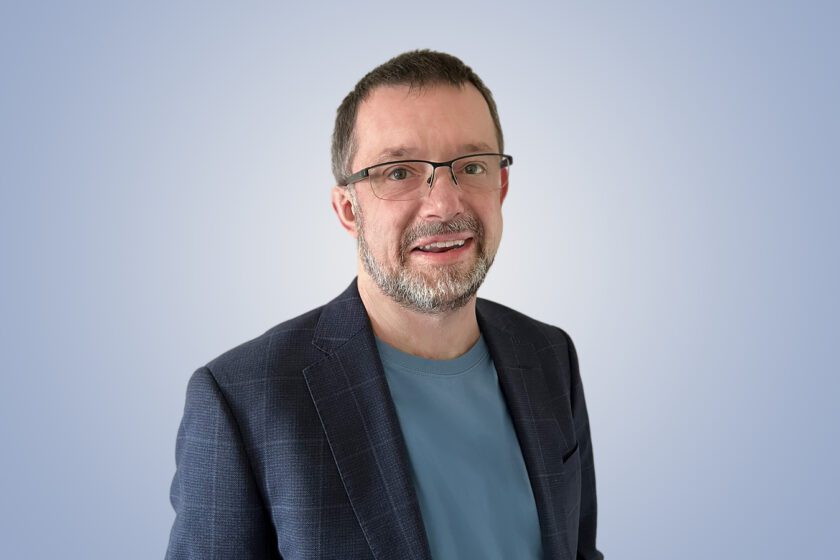
Rock Voyer, P.Eng., M.Eng.
Rock Voyer spent the first part of his career providing multi-million-dollar project management and leading sustainable process initiatives at Molson Coors Canada reducing energy usage by 42% and water consumption by 45%. Deeply experienced in process, building infrastructure, utilities, energy savings, and product innovation, Rock now serves as a Senior Project Engineer for Salas O’Brien. Contact him at [email protected].
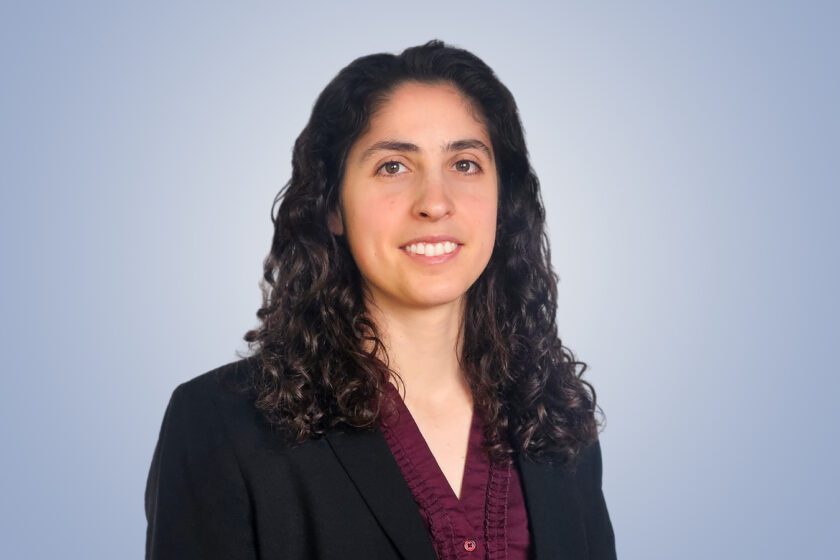
Mireille Sayad, P.Eng.
Mireille Sayad is a seasoned process engineer specializing in food and beverage manufacturing, focusing on system design, project management, and sustainable initiatives. She oversees every stage of a project—from definition and planning to detailed engineering and construction supervision working for some of the best-known brands in the world. Mireille serves as a project engineer & project manager at Salas O’Brien. Contact her at [email protected]
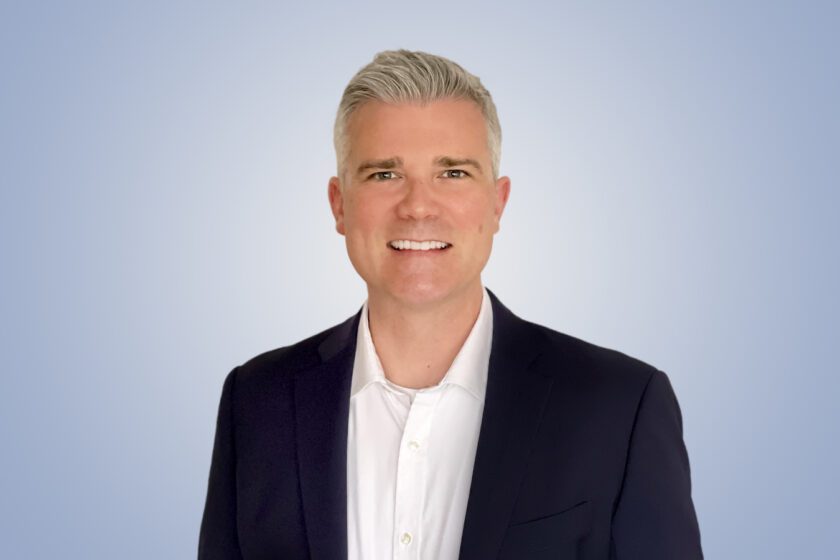
Rick Humphries, PE
Rick Humphries is an industry expert bridging the technical, operational, and financial components of energy infrastructure projects. With career experience working from all three perspectives, he is an invaluable resource to owners and project teams in a time of transitioning energy sources, systems, and strategies. Rick serves as a Senior Vice President and a Director of Development at Salas O’Brien. Contact him at [email protected]
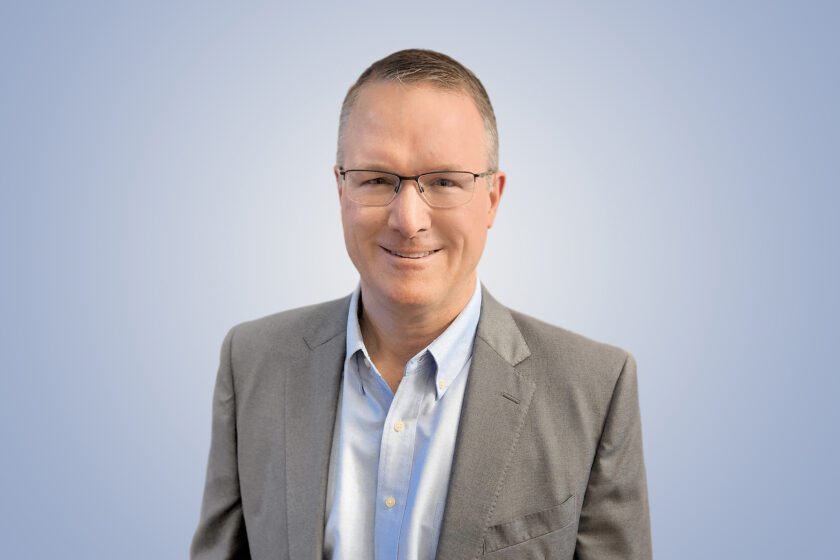
Jody Zepnick
Jody Zepnick has 30+ years of industrial automation experience, primarily in the dairy, paper, and food industries, working with clients from small manufacturers to Fortune 100 companies. Founder of Zepnick Solutions—an industry leader in robotics and automation for manufacturing—Jody lead the team to merge with Salas O’Brien in 2024. Jody serves as a Principal for Salas O’Brien. Contact him at [email protected].